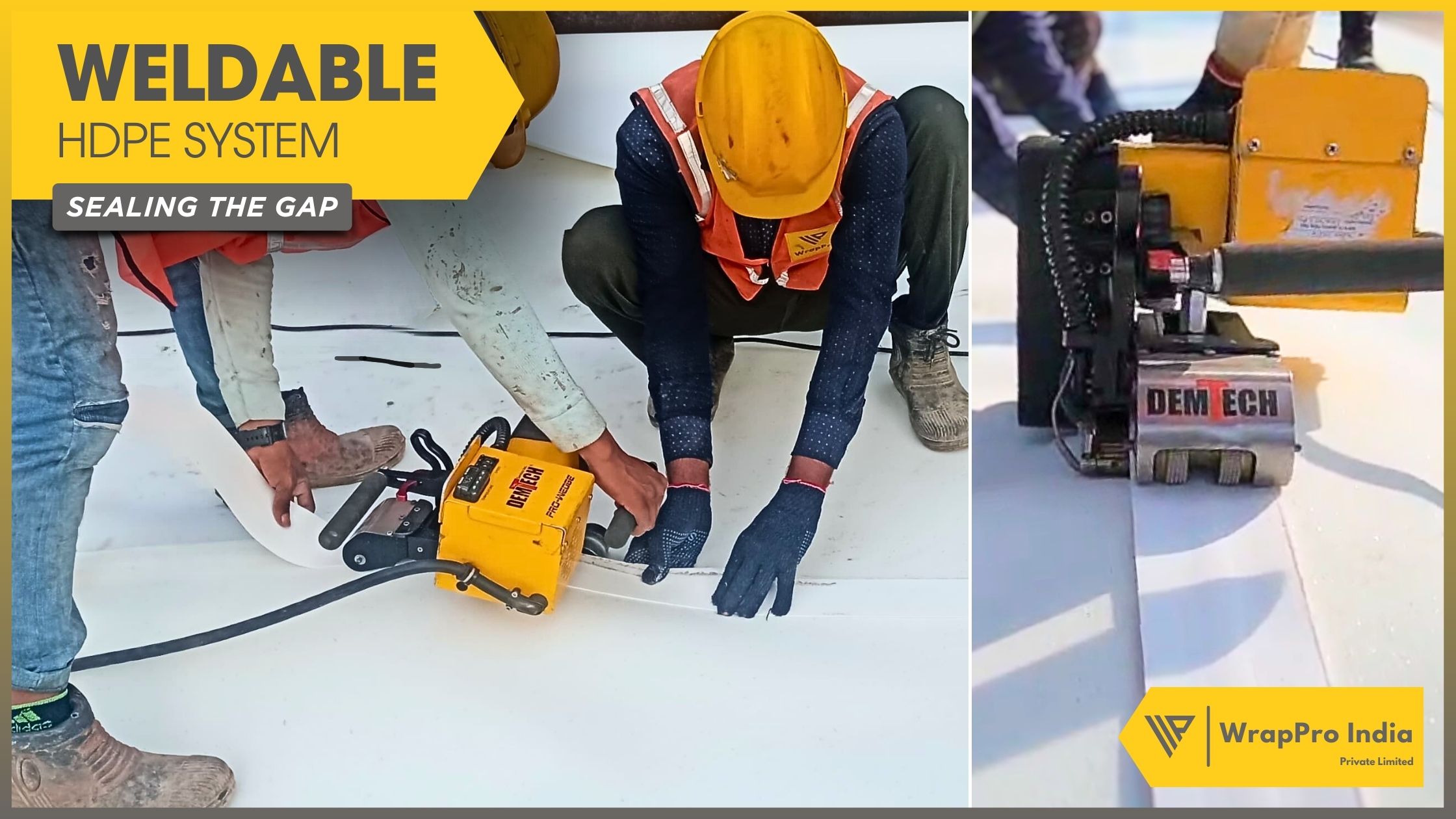
Sealing the Gap: The Introduction of Weldable HDPE in Basement Waterproofing
In the complex realm of basement waterproofing, the advent of High-Density Polyethylene (HDPE) membranes marked a significant milestone, offering a robust solution to protect underground structures from water ingress. However, as we discussed in our previous article titled “Best System, Trained Applicator, Yet Basements are Leaking,” the weak spot of HDPE Membranes has been the vulnerability of Overlaps or Seams to failure. This critical issue has underscored the pressing need for ongoing innovation and has highlighted the urgency for developing solutions that are not only robust but also consistently reliable.
What exactly is the Issue with Seams Failure?
Ensuring that seams are properly installed and protected is crucial for the overall effectiveness of the waterproofing strategy, aiming to prevent leaks and extend the lifespan of the structure. This necessity stems from the fact that seams are essential points where two sections of waterproofing material overlap and are bonded to create a unified barrier against water entry. HDPE Membranes, while popular for their durability and chemical resistance, have a significant vulnerability at the seams.
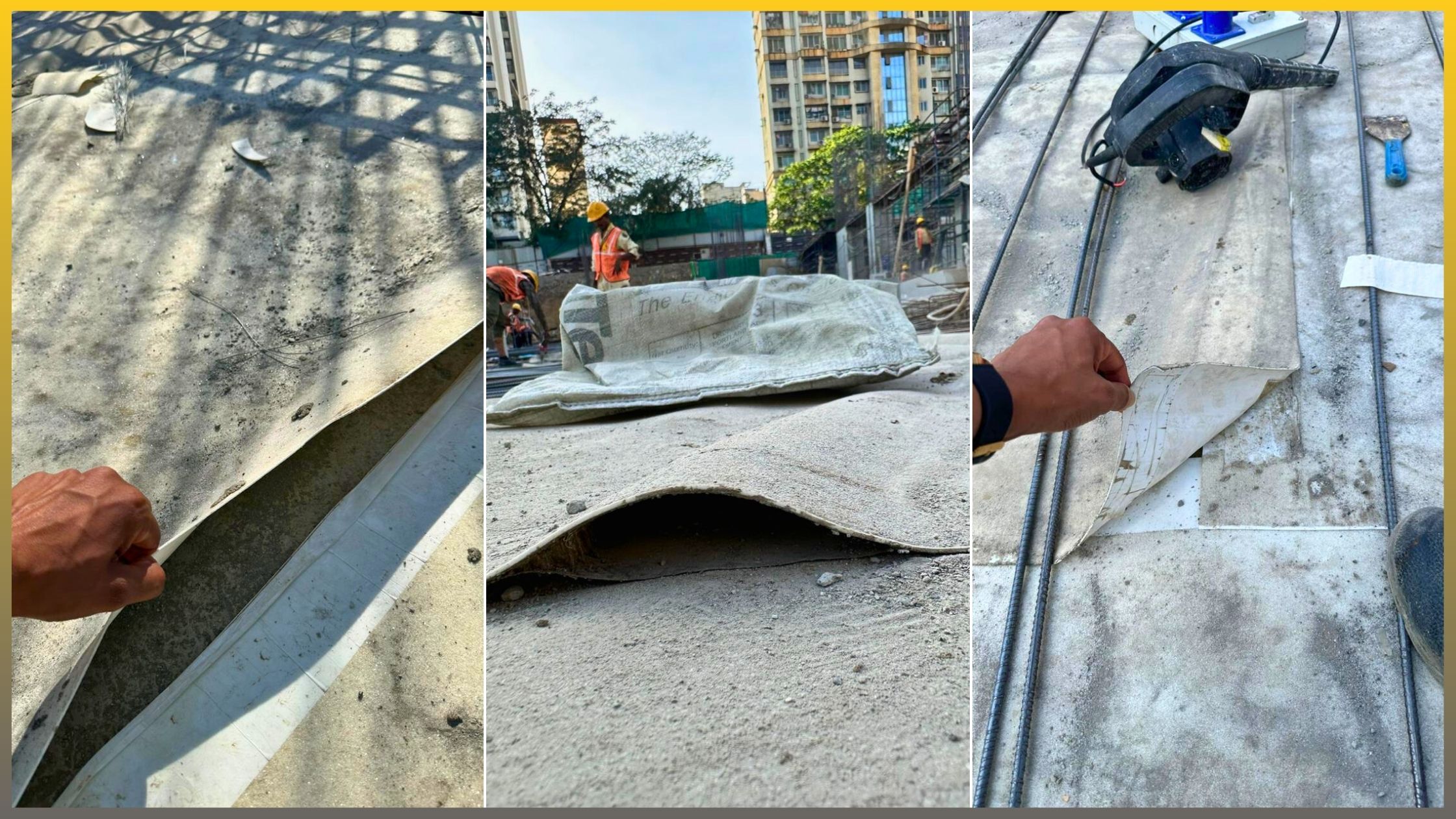
Despite their critical role, these junctures are susceptible to failure for various reasons, including incorrect application methods, challenging environmental conditions, and physical stress. If seams are not adequately secured, they become weak points through which water can penetrate, leading to leaks. The issue extends beyond the immediate area of the seam failure. Once water breaches this initial defense, it can spread beneath the membrane, affecting larger areas of the waterproofing system and potentially causing widespread damage.
This scenario highlights the complexity of seam integrity and the need for a comprehensive approach to enhance the reliability of waterproofing systems.
The Innovation of Weldable HDPE Membranes:
To tackle the concerning issue of seam failures, the waterproofing industry has embraced a revolutionary solution: Weldable HDPE Membranes. This innovation diverges from the traditional adhesive-based methods for sealing seams, employing a sophisticated welding technique that securely joins the membrane overlaps.
The welding process is carried out using a high-end, specialized machine designed explicitly for HDPE welding. This equipment applies precise heat to the membrane overlaps, causing the material to meld together upon cooling, forming one continuous, seamless layer.
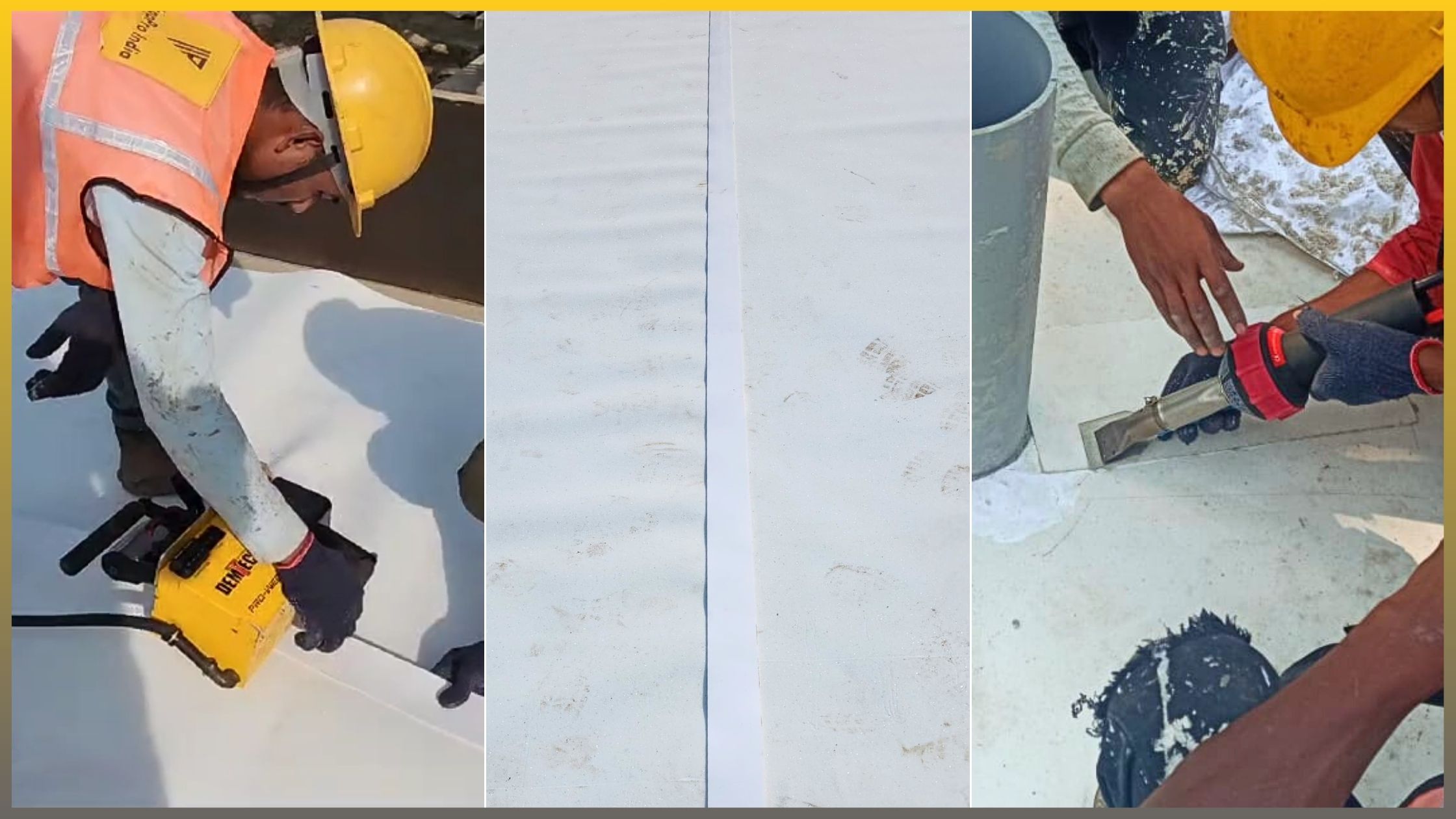
This advanced method of fusing the membrane sections ensures a seamless and highly effective barrier against water, drastically reducing the possibility of seam failures that have plagued adhesive-based systems. With the introduction of machinery designed specifically for the task, Weldable HDPE Membranes offer a stronger, more reliable connection between membrane sections, enhancing the overall durability and effectiveness of waterproofing systems.
Advancing Innovation and Quality in Waterproofing:
The introduction of Weldable HDPE Membranes signifies the waterproofing industry’s continuous dedication to quality and innovation. This advancement is a key component of a wider initiative aimed at addressing persistent challenges with cutting-edge technological solutions. At WrapPro India, our role as a professional waterproofing contractor involves integrating these innovative solutions to advance our services. This adoption reflects our commitment to improving service standards and aiding in the sector’s progress towards enhanced organization, professionalism, and a focus on meeting customer needs.
Looking Ahead: The Need for Comprehensive Protection Against Damage.
Despite claims of HDPE Membrane’s high durability and resistance to damage, the practical experiences at construction sites suggest a vulnerability to physical damage from construction debris such as steel rods and other sharp objects. This reality underscores the need for enhancements that go beyond the theoretical strengths of HDPE membranes to deliver tangible, on-site self-protection.
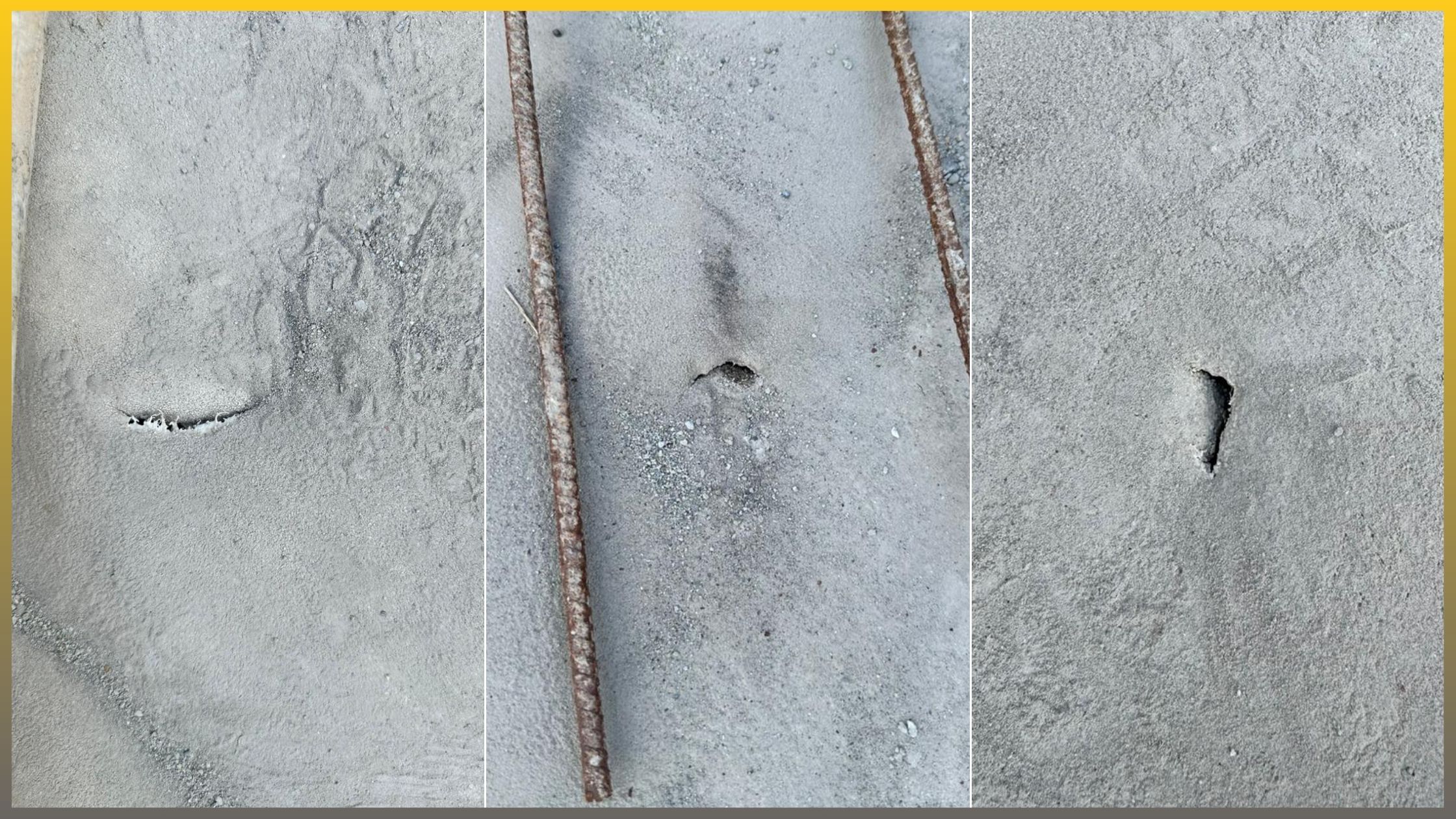
Future innovations must focus on increasing the membranes’ ability to withstand the interim period between installation and the casting of the concrete, which is a critical exposure window. Aligning the technological development of these membranes with the practical demands of construction sites will be key to ensuring that the waterproofing systems remain intact and functional throughout the building process and beyond.
In conclusion, the journey of enhancing basement waterproofing techniques has been both challenging and rewarding. As we move forward, the focus remains on not just addressing current challenges but anticipating future needs. The path ahead is clear: by embracing innovation, fostering quality, and anticipating the evolving demands of construction environments, we can ensure that our waterproofing solutions remain effective, reliable, and ahead of their time.
“Genius is one percent inspiration and ninety-nine percent perspiration.”
– Thomas Edison.
This insightful observation by Edison underscores the essence of innovation in overcoming challenges, such as those faced in the waterproofing industry, reminding us that persistence and hard work pave the way to ground-breaking solutions.
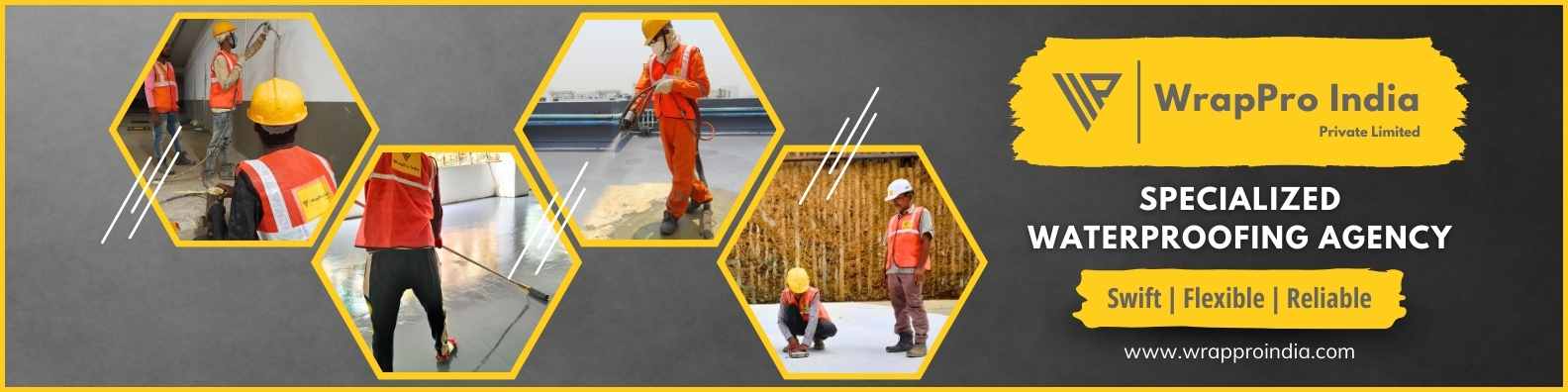