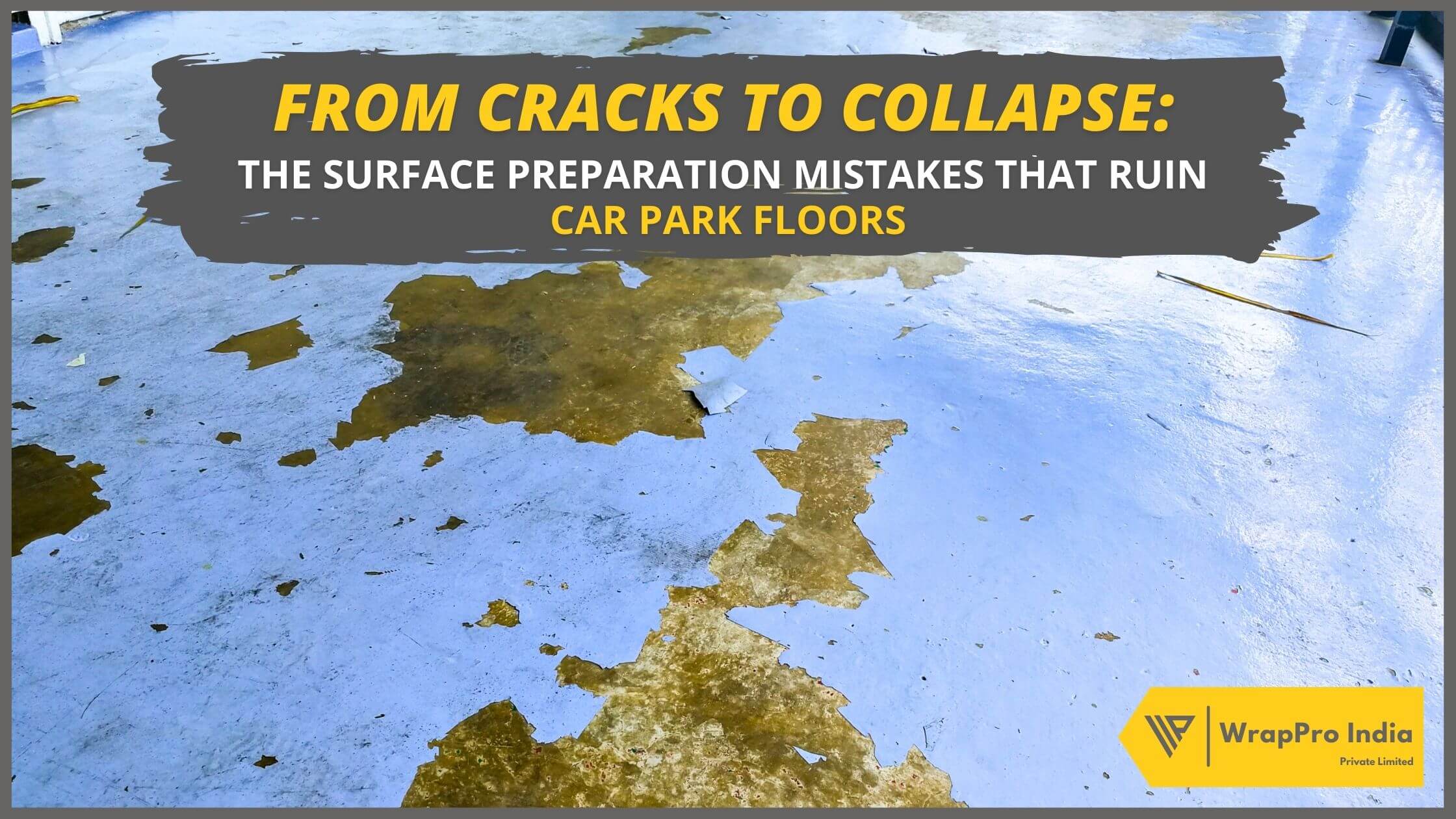
From Cracks to Collapse — The Surface Preparation Mistakes that Ruin Car Park Floors
The success of a car park flooring system is intrinsically tied to the quality of its initial surface preparation. As much as proper preparation can set the stage for a durable and visually appealing floor, negligence during this phase can lead to a cascade of problems that culminate in flooring system failures. This article serves as a comprehensive guide to help you navigate the complexities of surface preparation for car park flooring by spotlighting errors to avoid for long-lasting results.
The Critical Errors in Surface Preparation for Car Park Flooring & their Consequences.
1) Overlooking the Basics of Initial Cleaning
Error: Failing to adequately clean the surface before commencing with further preparation can have dire consequences. Skipping this step is often justified as a time-saving measure to fast-track projects. However, an unclean surface is never an ideal substrate for further treatments.
Consequence: Neglected contaminants like grease, dust, and debris can compromise the adhesive quality of the coatings. This neglect can pave the way for problems such as peeling or cracking over time.
2) Assuming the Surface Is Dry Without Testing
Error: Opting to forgo moisture tests based solely on visual assessment is flawed reasoning. Even seemingly dry surfaces can hold hidden moisture that jeopardizes the flooring. Moisture tests provide empirical data that visuals simply cannot.
Consequence: Undetected moisture can interfere with adhesive qualities and disrupt the car park flooring’s integrity. Furthermore, it can be a breeding ground for mold and mildew beneath the flooring system.
3) Cutting Corners on Crack and Gap Sealing
Error: Using inappropriate materials or techniques for filling cracks and gaps may save time initially but will cost more in repairs later. Often, the urgency to complete the project leads to such compromises. A durable car park floor requires meticulous attention to even minor details.
Consequence: These improperly sealed areas can become weak points in the flooring, inviting further cracking and moisture infiltration, thereby affecting the overall longevity of the car park flooring system.
4) Neglecting Proper Surface Profiling
Error: Ignoring the specifics of surface profiling can be costly both in terms of material wastage and reduced effectiveness of adhesion. Surface profiling is not a one-size-fits-all operation; it varies depending on the type of flooring material used. Different materials require tailored profiling for optimal results.
Consequence: The absence of a proper “tooth” for the coating to adhere to can lead to issues such as delamination and flaking, causing both aesthetic and functional problems in the car park flooring.
5) Ignoring the Necessity of pH Level Checks
Error: Overlooking the importance of testing surface pH levels is a critical mistake. This lapse usually stems from a lack of understanding about the diverse chemical properties of flooring materials. Flooring materials and coatings for car parks have specific pH compatibility ranges for optimal performance. The pH scale ranges from 0 to 14, with 7 being neutral. A pH level less than 7 is considered acidic, and a pH greater than 7 is considered alkaline or basic.
Consequence: Unsuitable pH levels can cause chemical imbalance with the coating. This could result in discoloration and a weakened car park flooring system, affecting both the appearance and durability.
6) Avoiding Investment in Specialized Tools
Error: While general-purpose tools might be more accessible, they lack the precision that specialized tools bring to surface preparation for car park flooring. Specialized tools are designed to ensure that surface preparation meets the necessary standards for optimal coating adherence.
Consequence: Such an approach can result in uneven surface texture, which in turn affects the uniformity and durability of the applied coatings, negating any initial savings in tool costs.
7) Skipping Crucial Time Allocations in Preparation
Error: Not allowing sufficient time for essential steps, like curing in concrete repairs or drying after cleaning, can be problematic. The rush to move on to the next phase often clouds better judgment. Each preparation phase has its own time requirements for a reason.
Consequence: A hurried preparation process can lead to a host of issues, from poor adhesion to uneven coatings. These shortcuts compromise the durability and longevity of the car park floor.
8) Disregarding Manufacturer-Provided Guidelines
Error: Ignoring or not thoroughly following the guidelines provided by material manufacturers for car park flooring is a grievous mistake. It’s crucial to remember that manufacturers have in-depth knowledge of how their products should be used for optimal results. These guidelines are built on exhaustive product research and testing.
Consequence: Non-compliance could lead to immediate problems like poor adhesion and can even void warranties, leading to unnecessary future costs and complications.
In summary, each point covered in this article is not just a fleeting consideration but a topic substantial enough to warrant its own dedicated article. From the intricacies of initial cleaning to the science behind pH level checks, every aspect of surface preparation has multiple layers that can significantly impact the longevity and durability of your car park flooring system.
As the saying goes,
“To build high, you must dig deep.”
In the context of car park flooring systems, this means that the foundation—the surface preparation—is as vital as any subsequent layer.
By adopting a meticulous approach to surface preparation for car park flooring, you can significantly lower the risks associated with flooring failures, thereby safeguarding your investment for years to come.
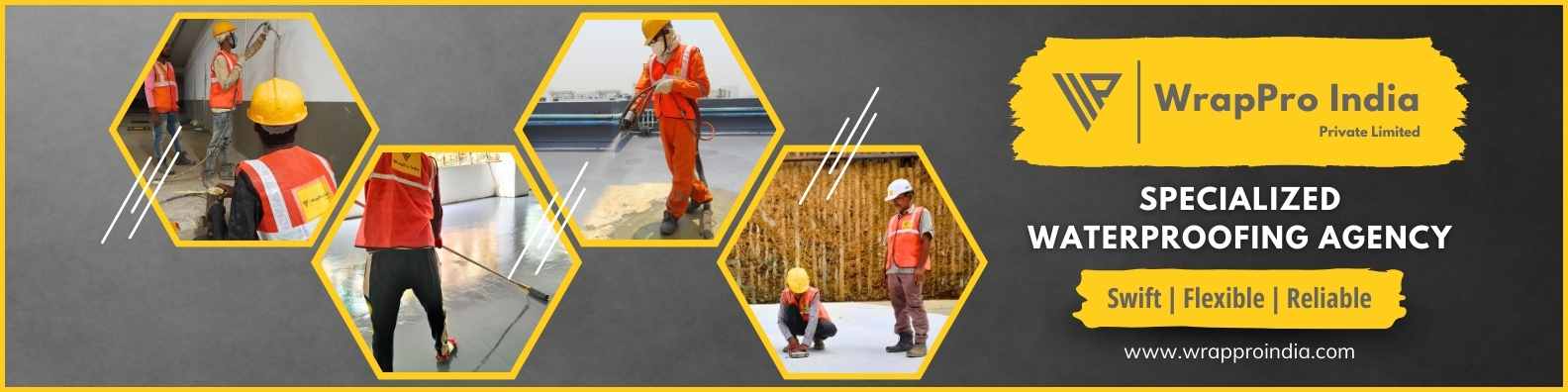